Traditional Techniques and Craftsmen
Craftsman
Each step in making Owari Cloisonne requires advanced skills, typically handled by specialized craftsmen dedicated to specific tasks. Historically, in Owari Cloisonne, different stages of the process were carried out by specialized companies. Over time they have dwindled in number, making it increasingly difficult to pass on the cloisonne techniques. Ando Cloisonne believes preventing the exquisiteness of cloisonne craftsmanship die out is essential. They are committed to transferring skills cultivated over many years from artisans to the next generation, continuing to preserve cloisonne as a proud Japanese traditional technique. The following introduces cloisonne, practiced by experienced craftsmen and passed on to the next generation.
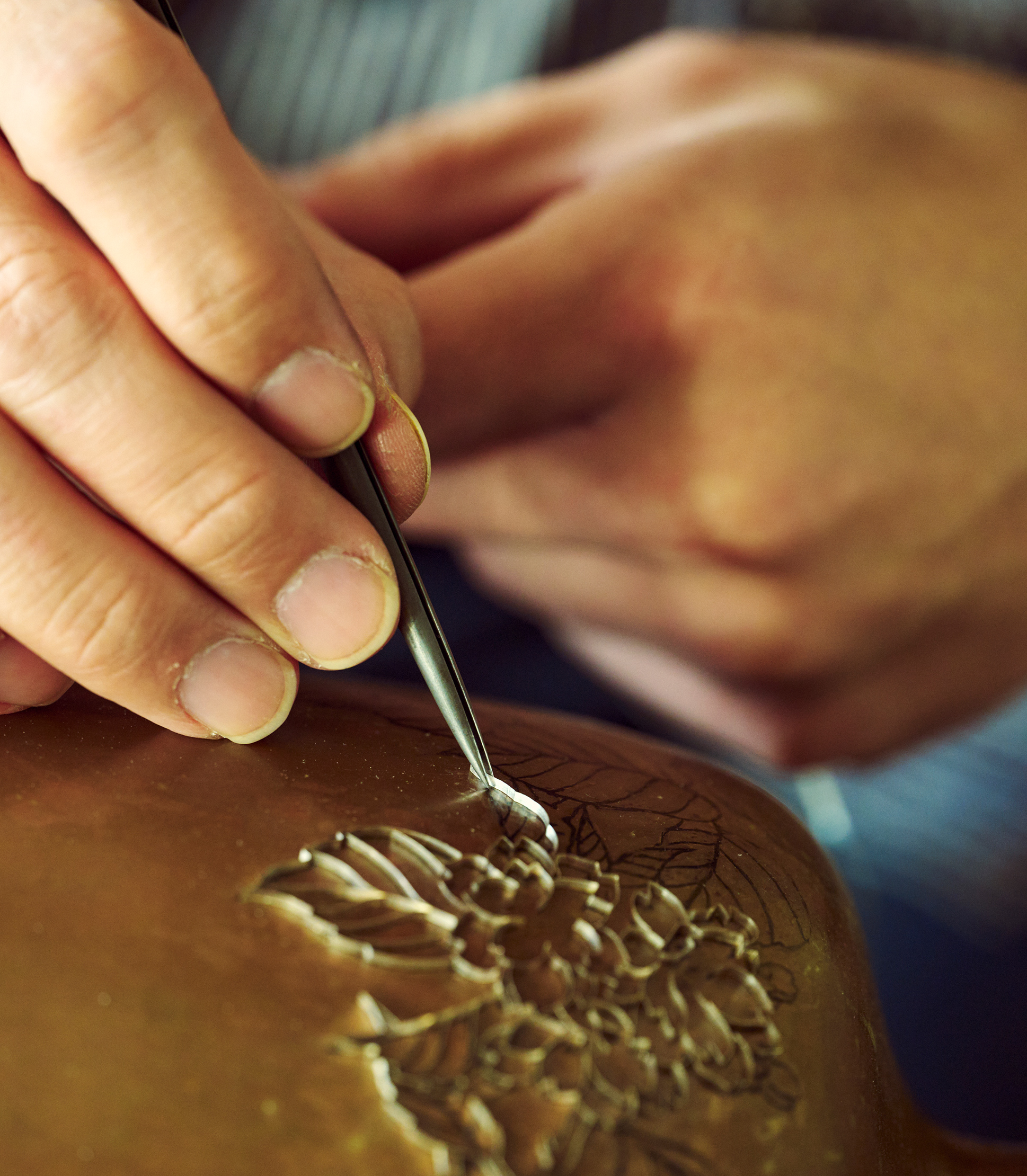
The Process of Making Cloisonne
Shaping Metal to Form the Piece
The base for Owari Cloisonne is shaped copper plates. Ando Cloisonne employs two main methods: Hera-shibori, where the metal is rotated and shaped using a spatula, and electroforming when making molds using electroplating technology.
The metal spinning (Hera-shibori)
Electrocasting
Transferring the Image Design to the Base
The process involves transferring a pattern onto the surface of the base. There are two main methods for underdrawing: directly drawing with ink on the base, and first, applying a white enamel, then doing an initial firing before drawing. Recently, some have started to skip this process by using a plastic mold with a pattern carved into it and applying the enamel through it.
Setting Silver Wires for Edging
Following the ink outline, silver wires are attached with an adhesive. These wires eventually become the main lines of the pattern and appear on the surface. Each silver wire is bent by hand to create the desired shape. Wiring requires a high level of skill to ensure there are no gaps between the wire and the curved surfaces of the base.
Applying Glass Enamel and Adding Color
After the silver wire inlay is complete, a enamel is applied between the lines on the metal base. The number of enamels prepared depends on the design but can include dozens of varieties. As enamels cannot be mixed like paint, each subtle nuance of color needs to be created separately. Moreover, since the color changes upon firing, years of experience are needed to anticipate the final hues. This process remains difficult to mechanize and is meticulously carried out by experienced artisans.
Melting and Fusing the Applied Enamel onto the Base
After enameling, the pieces are fired in an electric kiln at temperatures between 700°C to 800°C for about 10 to 15 minutes. The firing temperature and duration vary depending on the shape of the piece and the type of enamel used. The firing process melts the powdered enamel, creating a difference in height between it and the metal lines. Several rounds of enameling may be repeated until the height of the enamel aligns with the metal lines. Different methods, such as layering different colored enamels to create a sense of transparency or applying thicker enamel to add dimension, are used to achieve the final appearance.
Smoothing the Surface and Refining the Design
The surface of the fired Owari Cloisonne is uneven at this stage, with differences in height between the metal lines and the enameld areas. Polishing is done to smooth out these irregularities. Water is applied to the surface, and it is polished using grinding stones, then further refined using charcoal or tin oxide to restore its luster. As polishing progresses, the contours of the Owari Cloisonne design, marked by the metal lines, become more distinct. In recent years, industrial-grade diamonds with high hardness have also been used for polishing.
Applying a Rim to Exposed Base Areas
The top and bottom edges, which remain unprocessed during polishing, expose the copper base. In this step, a protective rim made of silver or silver plating is applied to these parts. For example, in the case of a vase, silver or silver-plated rings are fitted at the mouth and the base to finish it.
Preserving Traditional Techniques
The techniques involved in each stage of cloisonne production have reached a point where they might cease to exist due to the dwindling number of specialized artisans over time. Ando Cloisonne is committed to preserving these valuable techniques. They have welcomed artisans with these rare skills into their company, working alongside machines, and are dedicated to passing these skills on to the next generation.
-
Craftsman Dialogue 01 The metal spinning (Hera-shibori)
-
Craftsman Dialogue 02 Electrocasting
-
Craftsman Dialogue 03 Wires
-
Craftsman Dialogue 04 Enameling